Concrete is so useful!
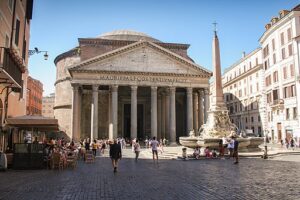
I KNOW! That’s why it’s so hard to admit! Concrete, in a variety of forms, is regularly touted as one of the main ingredients for our most energy efficient and resilient buildings.
Architects and builders know it holds conditioned air (heated OR cooled) oh so well! It’s just so good for making airtight buildings that retain their thermal mass well when properly insulated and air sealed.
Better still, it’s very resilient to the increasing number of windstorms that can lay waste to traditional wood frame and brick homes and buildings while also being much harder for fire, mold, and pests to get through. Witness the fact that Europe is still dotted with concrete structures built by the Romans.
It fits the mold in oh so many ways . . .
But it gives the planet gas!
Unfortunately, one of the green building industry’s most common and useful materials requires a production process that both pollutes and warms our atmosphere at a time when we’re trying to avoid further contribution to climate change. Often, buildings built to high energy use and environmental standards depend on these carbon-intensive materials. This means that these buildings release less carbon into the atmosphere once built and lived in, but release more in the making of their components.
For example, a measurement of embodied carbon in a 15-story reinforced concrete apartment building in Atlanta, Georgia gave a value of 233 kilograms of carbon dioxide equivalents per square meter (kgCO2e/m^2 for the mathematically inclined). A similarly sized timber building was shown by the same study to contain considerably less embodied carbon.
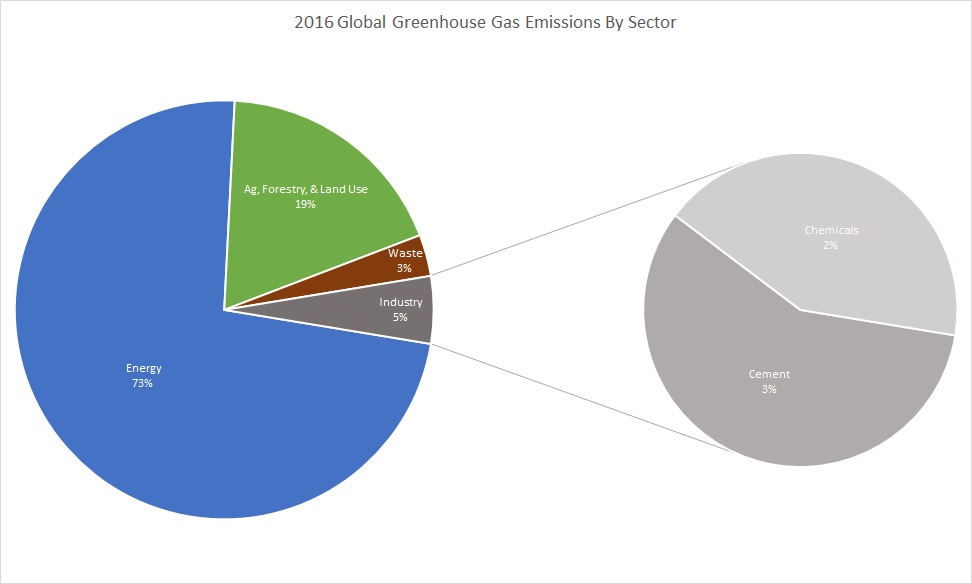
The chart above shows the percentages of greenhouse gases that came from the world’s different commercial sectors in 2016. Out of a grand total of 49.4 million metric tonnes of greenhouse gases (measured in carbon dioxide equivalents), the portion from the chemical process of creating concrete’s key ingredient alone comprises 3%, which is 1.48 million metric tonnes. This number is arrived at before including the energy needed to heat the initial aggregate to 1400 degrees Celsius, which would add another significant percentage of greenhouse gases.
This creates an obvious dilemma for the green building community: how do we build energy efficient buildings that are supposed to help the planet if the main building material needs us to fart more greenhouse gases to create it?
So what do we use instead?
The commonness and usefulness of concrete make it difficult to replace as a cornerstone building material. The good news is that alternatives are coming. While their widespread adoption is in its relative infancy, the recognized need for new options is spurring sustainable developers to start using alternatives early.
Here are a few that have been used in existing buildings and projects:
Autoclaved Aerated Concrete (AAC)
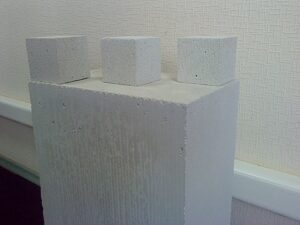
AAC shows that sometimes it makes sense to reinvent the wheel, or in this case, the brick. AAC differentiates itself from typical concrete by using far less cement—concrete’s main and most resource intensive ingredient—and more air than regular concrete. Better still, its curing process uses non-toxic ingredients for its mix, and steam for curing.
The combination makes AAC a much greener solution, particularly for single-family homes or smaller business locations. The brick-like construction also lends itself to larger blocks or shapes that may make construction faster and cheaper than pouring concrete on site, too.
Cross Laminated Timber (CLT or XLT)
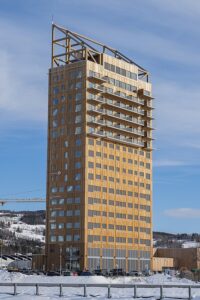
Don’t run away yet! Yes it’s wood, but this wood is farmed for specific use. As a building material, CLT distinguishes itself with layering and treatment that allow this relatively lightweight material to be fire and element resistant. Better still, one study found that for every metric ton of timber used, roughly two metric tons of carbon emissions are saved at the production level. Even more carbon may be saved if building remnants are turned to biochar for carbon sequestration at the end of the CLT building’s life.
Moreover, the layering and chemical treatment create panels that are both light enough for easier and roomier construction than concrete and steel, while being strong enough to support small skyscrapers like the one pictured here in Norway.
While in its relative infancy in the United States, our Canadian neighbors are adopting it quickly. It’s only a matter of time before more CLT buildings sprout here.
Pre-fabricated Modular Construction
Modular construction maintains a relatively low carbon footprint by building modules in a factory. This eliminates a lot of the waste associated with typical on-site construction, and largely reduces the use of concrete, if not eliminating it outright in cases where concrete is not the main structural material.
The embodied carbon to be mindful of with this construction type is decreased in module manufacture, and and otherwise limited to transportation and energy used in construction. It’s often cheaper, too!
In the case of the Stack located at 4857 Broadway in the Inwood neighborhood of Manhattan, modules were lifted in place, bolted together, and reinforced after being positioned. This not only saved on the use of more resource-intensive materials but made construction of this building quicker and more efficient as well.
Construction materials and methods are expanding to cut carbon emissions as the demand for living space grows with our population. Still, until these techniques scale up in their usage, poured concrete will likely remain a central pillar among effective building materials.
So what can you do?
Well, that depends on who you are and where you fit:
- If you live in the building science and development worlds like I do, you find the pioneering architects that want to do more of this work near you and introduce them to developers that want a way to either be greener or stand out (hopefully by being greener).
- If you’re thinking about building your own home, look into the options to use these materials and techniques to build a house. AAC and modular construction would be the easiest to do here in the United States, but there are resources for CLT too.
- If you’re renting and have found a building with a build like this, or want to find one, a little bit of research would go a long way. Better still, when you find such a building, ask the ownership. They’ll not only be very happy to discuss the details with you, but it will encourage them to build more like that in the future.
Let’s build a greener world!
There are two reasons why manufacturing cement releases a lot of carbon: the combustion of fossil fuels typically used to heat the kiln, and the chemical reaction that releases carbon stored in limestone.
As a professional concrete contractor in Albuquerque, I am excited to see the potential growth of new construction materials and methods that can reduce carbon emissions. While poured concrete will likely remain a pillar of building materials for some time, these new approaches are definitely worth exploring. That being said, it is important to consult with a professional before attempting to use these materials and methods for construction. With the right knowledge and expertise, these materials can be used effectively to create strong, sustainable structures that will benefit both our environment and our communities. Thanks for this great overview of what is available!
Thank you for the useful blog! I didn’t realize there were so many types of concrete and even more under R and D. This is very helpful for consumers and even some contractors.
http://www.certifiedconcreteprosin.com
Yeah I agree, it was a solid and yet funny way to look at concrete. https://www.concretecontractorsmilwaukeewi.com
I’m fascinated with AAC! I believe there is a ton of potential there. Great post!